Tool and die manufacturing might sound technical, but it’s a vital part of just about everything we interact with in our daily lives. From the car we drive to the appliances we use, tool and die makers play an essential role in ensuring the parts that make up these products are created with accuracy and precision. And trust me, without their expertise, many of the things we take for granted wouldn’t even exist!
Let’s break down what tool and die manufacturing is all about, explore its significance, and look at why it’s so important across industries. I’ll throw in a few fun facts that might surprise you along the way.
What Is Tool and Die Manufacturing?
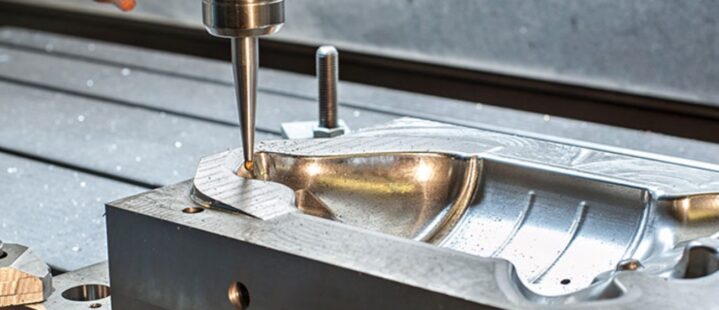
At its core, tool and die manufacturing revolves around creating specialized tools, molds, and dies used to form and shape materials, most often metals. These tools enable manufacturers to produce consistent, high-quality parts that meet strict specifications. Think about it—when you need a bolt or a specific car part, it has to be identical every time. No one wants their car falling apart because one bolt is too loose or one part is too big, right? You can learn more about the process of tool and die manufacturing at runsom.com.
Tools: In this world, “tools” refer to the specialized pieces of equipment used to shape, cut, or form metal and other materials. Toolmakers craft the molds, jigs, and fixtures that enable production lines to work smoothly and efficiently.
Dies: A “die” is a special tool designed to cut or shape material. Dies are typically used in stamping and forging operations, where raw materials are pressed into a specific shape or form. Think of a cookie cutter, but much more precise—and it’s used to shape metal rather than dough.
Why Precision Matters So Much
I can’t stress this enough: accuracy is everything in tool and die manufacturing. Even the tiniest mistake can cause huge issues down the line. Imagine the chaos if thousands of parts are produced with just a millimeter off! In industries like automotive, aerospace, and electronics, where safety and performance are paramount, this kind of precision isn’t just desired—it’s required.
When we talk about precision, we’re referring to measurements that are often in microns (one-thousandth of a millimeter). This is mind-bogglingly small. To give you some perspective, a single human hair is around 70 microns thick. So when tool and die makers are asked to create a tool with tolerances of 10 microns, that’s beyond delicate work.
How Precision Impacts Industries:
- Automotive: The parts inside your car—everything from the transmission to the engine block—are produced using tools and dies. If any of these parts aren’t made to exact specifications, it could affect performance, safety, or longevity of the vehicle.
- Aerospace: In an industry where the smallest flaw can lead to disaster, precision in tool and die manufacturing is absolutely critical. Every part on an airplane or spacecraft must be perfectly formed to ensure safety and function.
- Consumer Electronics: The circuit boards, connectors, and other tiny components in your phone or laptop require incredible precision. The tools and dies that produce them must be designed to handle the intricate details of these small-scale parts.
Different Types of Tool and Die Making
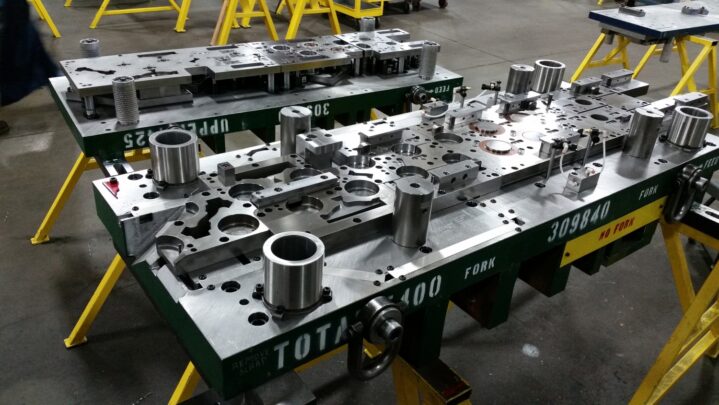
Depending on the job, different types of tools and dies are used. Let’s explore a few of the major types:
Stamping Dies
These are used to cut or shape metal through a process called stamping. A stamping die is essentially a metal mold that presses into the raw material (often sheet metal) to create a specific shape. It’s like pressing a stamp into soft clay to leave an imprint, except much more complex.
Stamping dies are crucial for industries like automotive manufacturing, where large numbers of identical parts are required. They are used to create everything from car doors to tiny metal clips used in electronics.
Injection Molds
Injection molding is another popular method, and it’s commonly used for producing plastic parts. You’ve probably heard of injection-molded toys or containers. The concept is fairly straightforward: molten plastic is injected into a mold where it cools and takes shape.
Toolmakers create the molds for this process, ensuring they can withstand the extreme heat and pressure of molten plastic while maintaining the intricate details of the final product.
Extrusion Dies
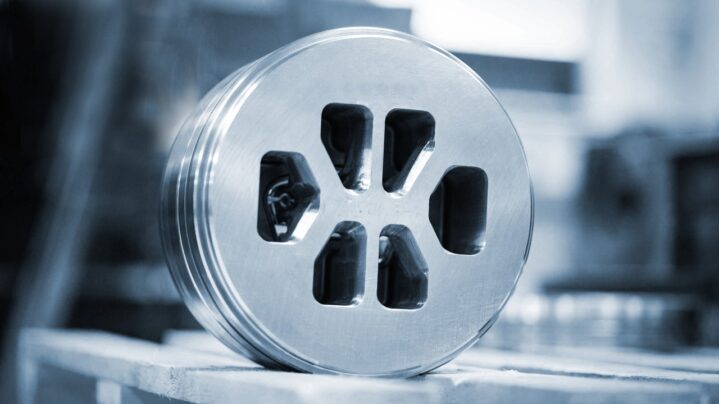
Extrusion is a process used to create objects with a fixed cross-sectional profile. Think about how pasta is made: dough is pushed through a mold to create different shapes like spaghetti, penne, or fusilli. Extrusion dies work similarly, but with materials like aluminum or plastic.
The extrusion die shapes the material as it’s forced through, creating things like pipes, tubes, or even window frames.
Progressive Dies
Now, here’s where things get interesting. Progressive dies are designed to perform multiple operations at once—cutting, bending, and shaping metal all in a single stroke of the machine. This makes the manufacturing process much faster and more efficient. Progressive dies are often used in high-volume production where speed and consistency are crucial.
What Goes into Tool and Die Making?
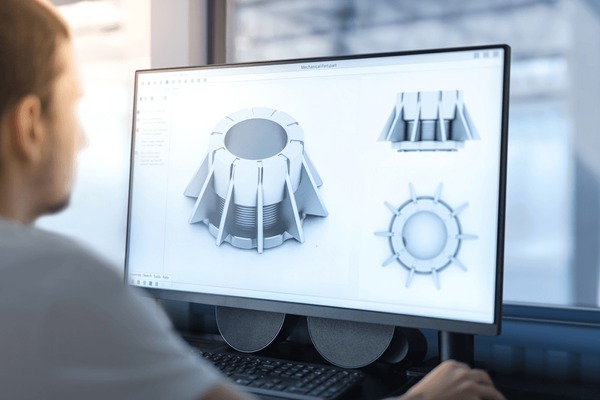
The skills required to become a tool and die maker are vast, and the process itself is incredibly detailed. At its heart, it’s a blend of artistry, craftsmanship, and technology. Here’s a quick look at the key components of the process:
1. Design and Planning
Before anything is created, it’s carefully designed using computer-aided design (CAD) software. This allows manufacturers to create precise blueprints and 3D models of the tool or die.
2. Material Selection
Tool and die makers must choose the right material for the job. Most dies are made from tool steel, a material known for its hardness and ability to retain its shape even after repeated use. Other materials like carbide or ceramics may be used for specific applications.
3. Machining and Fabrication
Once the design is finalized and the materials are selected, the actual fabrication process begins. This involves using specialized machines—like CNC (computer numerical control) machines, lathes, and milling machines—to cut, shape, and form the tool or die.
4. Assembly and Testing
Once the tool or die is fabricated, it’s assembled and tested to ensure it meets the required specifications. Testing is a critical step because any flaw in the tool could lead to defects in the final product.
5. Maintenance
Finally, tool and die makers are responsible for maintaining their creations. Over time, tools and dies wear down from repeated use, and regular maintenance is necessary to keep them functioning correctly. This can involve sharpening, repairing, or replacing certain parts.
In Summary
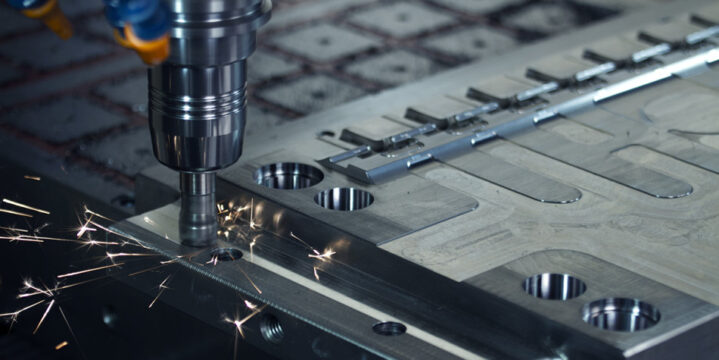
In the end, tool and die manufacturing is about it’s about enabling industries to produce the high-quality, reliable products we use every day. It might seem invisible, but trust me, without tool and die makers, the world around us would look—and function—a lot differently.